روش آزمایش
قیر مورداستفاده در این پژوهش در شرکت نفت پاسارگاد تولیدشده بود (جدول شماره 1). امولسیفایرهای کاتیـونی از لیگـنین آمین و آلکیـل آمـین ساختهشده که از شـرکت Inter Chemical Srl ایتالیا تهیهشده است.
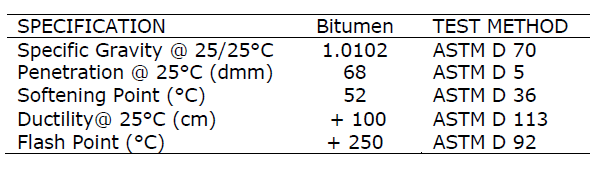
آمادهسازی امولسیون
قیر امولسیونی با استفاده از یک واحد آزمایشگاهی آمادهسازی امولسیون با مقادیر متفاوت امولسیفایر در PH مختلف (1، 1/3، 1/7، 2) و حلال به مقدار مختلف (0، 0/5، 1، 1/5 و 2 درصد) تهیه شد. در یک فرایند معمول مقدار مشخصی از امولسیفایر به یک پیمانه آزمایشگاهی حاوی 2 لیتر آبمعدنی 45 درجه سانتیگراد قرارگرفته بر روی یک صفحه حرارتی و دارای همزن برقی اضافه میشود. PH موردنظر با افزودن 37 درصد محلول هیدروکلریک اسید تنظیم میشود. از سوی دیگر، قیر در یک ظرف جداگانه تا دمای 140 درجه سانتیگراد حرارت دادهشده و مقدار موردنظر از حلال بااحتیاط به آن اضافه میشود. این دو فاز تحت همزن برشی بالا بهمنظور تولید امولسیون با یکدیگر مخلوط میشوند.
مشخصات امولسیون
1 تهنشینی
500 میلیلیتر قیر امولسیونی در یک استوانه شیشهای در دمای اتاق به مدت 5 روز قرار داده شد. سپس با استفاده از پیپت تقریباً 55 میلیلیتر نمونه از قسمت بالا و پایین امولسیون برداشتهشده و 50 گرم از امولسیونها در دو پیمانه ریخته شد. این پیمانهها به مدت 3 ساعت درون گرمکن در دمای 163 درجه سانتیگراد قرار داده شد. سپس آنها را از گرمکن خارج کرده و اجازه دادیم تا در دمای اتاق خنک شوند. پسازآن پیمانههای همدما شده با دمای اتاق را توزین کرده و درصد باقیمانده آن را به دست آوردیم. ثبات ذخیرهسازی امولسیون بهصورت تفاوت بین درصد باقیمانده از بالا و پایین آن تعریف میشود.
2 ویسکوزیته انگلر
این روش آزمایشگاهی، ویسکوزیته مخصوص امولسیون را مطابق با استاندارد ASTM D1665 تعیین میکند. ویسکوزیته انگلر بهوسیله اندازهگیری زمان موردنیاز برای جاری شدن حجم مشخصی از یک مایع (قیر امولسیونی) برای جاری شدن از یک لوله در دمای ثابت محاسبه میشود.
3 آزمون غربال
در این روش آزمایشگاهی بهطورمعمول مقدار 1 کیلوگرم از قیر امولسیونی را بر روی غربال 850 میکرومتر ریخته و بهآرامی با آب شستشو داده و پسازآن وزن مواد جامد باقیمانده بر روی الک محاسبه و درجه آن طبق استاندارد ASTM D244 تعیین میشود.
4 اختلاط سیمانی
این روش آزمایشگاهی برای تبیین قابلیت یک امولسیون قیر کند تنظیم برای اختلاط با مواد بسیار ریز با سطح بالا بدون شکست امولسیون طبق استاندارد ASTM D244 استفاده میشود.
————————————————————————————————————
برای مشاهده اولین مطلب درباره این موضوع برروی لینک زیر کلیک کنید: